Once it's completed, the breathtaking Spirit tower will be one of Australia’s tallest skyscrapers. Although its stunning design and dizzying height will no doubt grab all the headlines, there’s also a fascinating story to be told a lot lower down, where Keller is laying the foundations…
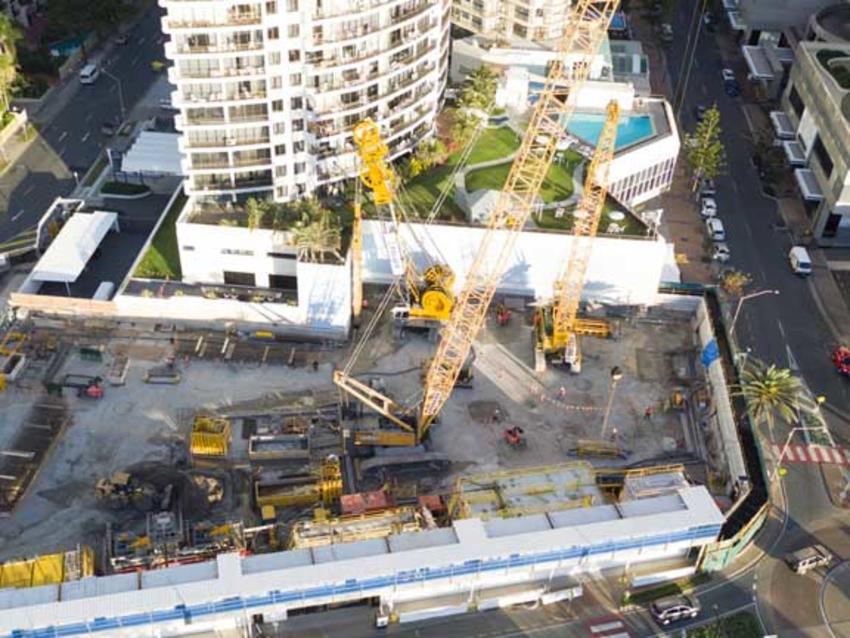
Renowned for its golden beaches, vibrant nightlife and stunning skyline, Surfers Paradise on Queensland’s Gold Coast is one of Australia’s most popular tourist destinations.
It’s also an area undergoing a huge construction boom, with billions of dollars pouring into hundreds of developments. One of the most high profile is a A$1.2 billion residential skyscraper that, at 297m, will be among the country’s tallest structures.
Developed by Chinese company Forise, Spirit will be an 89-storey beachfront high-rise with almost 700 luxury apartments. The tower will also feature three levels of retail space and a six-level basement.
Getting technical
After beating stiff competition, Keller was appointed as principle contractor for the foundation works. It was a fantastic win for the company, but a project that Forise spokesperson Jordan Hickey described as having “one of the most technical foundations in Australia’s history”.
The scope of works includes site investigation (17 boreholes); site clearance and set-up; 32 1,800mm diameter bored piles with precast plunge columns; a 250m diaphragm wall 45m deep to form the basement; and 53 barrettes for the core foundations. Twenty-six of the barrettes have steel plunge columns weighing up to 43 tonnes, allowing for a top-down construction – a method that allows the tower to be progressively constructed above ground at the same time as the basement floor slabs are laid below.
“Working closely with the client, their consultants and our Diaphragm Wall Global Product Team, we were able to design a scheme that met all the requirements for the extremely high loads imposed by a structure of this size,” explains Project Director John Spence. “We were also able to redesign the proposed barrettes, reducing their size and complexity and the need for out-of-hours working, all saving the client money.”
Specialist equipment
Keller’s part of the project is a year in and scheduled to finish in March. One of the biggest challenges so far has been the basement construction. “We opted for a diaphragm wall for the basement because of the onerous water tightness criteria specified by the client,” John explains. “In order to found it in the argillite rock, we decided to invest in a Bauer cutter from Germany. This has allowed the diaphragm wall to be cut into the rock and to create a water cut-off wall. Although a 0.6m thick wall would have sufficed, we decided on 0.8m to reduce the risk of seepage.
“Once the diaphragm wall is finished, the cutter will be modified to allow us to cut the deep barrettes required to support the building’s core, which will have loads of up 13,000 tonnes. The barrettes will be 1.5m wide and range in depth from 50m to 60m.”
Millimetre precision
Another challenge has been the massive steel plunge columns for around half of the barrettes. These columns, up to 37m long, had to be sourced from half way around the world in Luxembourg – the only mill in the world that makes the size of column needed for this type of project.
The concrete precast columns for the bored piles weigh around 25,000kg each and were installed using in-house designed frames to help meet the strict tolerances. An as-built survey showed that the team achieved an outstanding positional tolerance of 5-10mm and verticality tolerance of better than one in 250.
“Although it’s been very challenging at times, our robust design and attention to detail on site has meant that this project has run very smoothly so far,” says John. “We believe we’ve come up with an excellent solution and added real value for the client. Once again I think we’ve shown that, when it comes to high-profile projects such as these, Keller is more than capable of delivering.”