Keller is committed to reducing the carbon intensity of our work and increasing the quality and granularity of our carbon reporting.
Measuring carbon reduction
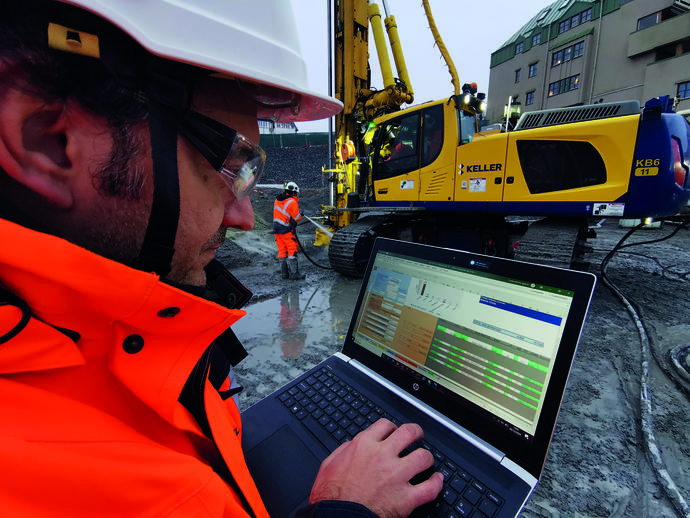
Keller has net zero targets which cover our direct emissions (Scope 1), our indirect emissions from electricity use (Scope 2) and emissions from business travel, waste disposal and material transport (Scope 3 Operational). These targets represent Keller’s commitment to the planet as we build the foundations for a sustainable future.
These absolute targets will help us mitigate future climate-related risks and recognise climate-related opportunities. We divide our emissions targets using the scopes set out in the GHG Protocol. These targets and our current performance are set out in the following section. The timeframe and lagging targets we set for each net zero commitment reflect the size and the level of control we have over each emission scope. To achieve these targets, we have set multiple internal leading targets, built around the carbon hierarchy.
This explains that, after we work through the hierarchy to eliminate, reduce and substitute emissions, we may offset our remaining emissions as a last resort.
Overall performance
This year, Keller’s overall Scope 1 and 2 emissions decreased. This mostly reflects a change in projects, with fewer carbon-intensive projects, like bucket mixing environmental remediation. In terms of the carbon intensity of our operations, emissions relative to revenue continued to fall and even outpace inflation. This reflects the range of carbon reduction and efficiency improvements implemented throughout the year, as well as improvements in revenue. It also means that Keller’s total relative emissions have either remained level or fallen every year since 2017.
Scope 1: direct emissions
Net zero by 2040
Scope 1 covers our direct emissions. These mostly arise from the fuel use of our rigs and Keller vehicles. Keller’s 2023 Scope 1 emissions have decreased since 2022. Scope 1 fuel emissions are highly dependent on the projects completed annually. With fewer projects in the US, as well as a drop off in our more carbon-intensive bucket mixing projects, Keller’s overall emissions have decreased. More importantly, the carbon intensity of our operations has decreased. This means we have continually decreased or maintained our Scope 1 emissions per £m revenue year on year since 2017. This reduction in relative emissions reflects a number of carbon reduction initiatives that were introduced this year. All these initiatives are needed to decouple our growing work from absolute Scope 1 emissions. Our initiatives are focused around the three stepping stones set out in our equipment decarbonisation strategy: efficiency improvements, alternative fuels and alternative equipment.
Read about our Scope 1 progress in our sustainability brochure.
Scope 2: Indirect emissions from electricity
Net zero by 2030
Scope 2 covers indirect emissions from the electricity we use. These emissions are mostly from office and maintenance yard operations, although 2023 also saw our first large sites run entirely from grid electricity. Nonetheless, Scope 2 is still the smallest of Keller’s three emission Scopes. Since these emissions do not significantly vary with the number of projects carried out, we only analyse absolute Scope 2 emissions. Location-based emissions are dependent on the average carbon intensity of energy generation in the countries in which we operate. Market-based emissions use the specific energy tariff for each of our offices and maintenance yards and therefore captures green energy tariffs.
Read about our Scope 2 progress in our sustainability brochure.
Scope 3: All other indirect emissions
Net zero for Operational Scope 3 by 2050
Scope 3 represents all other indirect emissions from Keller’s supply network. This means Scope 3 is the largest proportion of Keller’s emissions. To reflect where we believe we can have the most impact, we have set a net zero target for Operational Scope 3. This covers business travel, transportation of materials and waste disposal.
Read about our Scope 3 progress in our sustainability brochure.
The carbon hierarchy
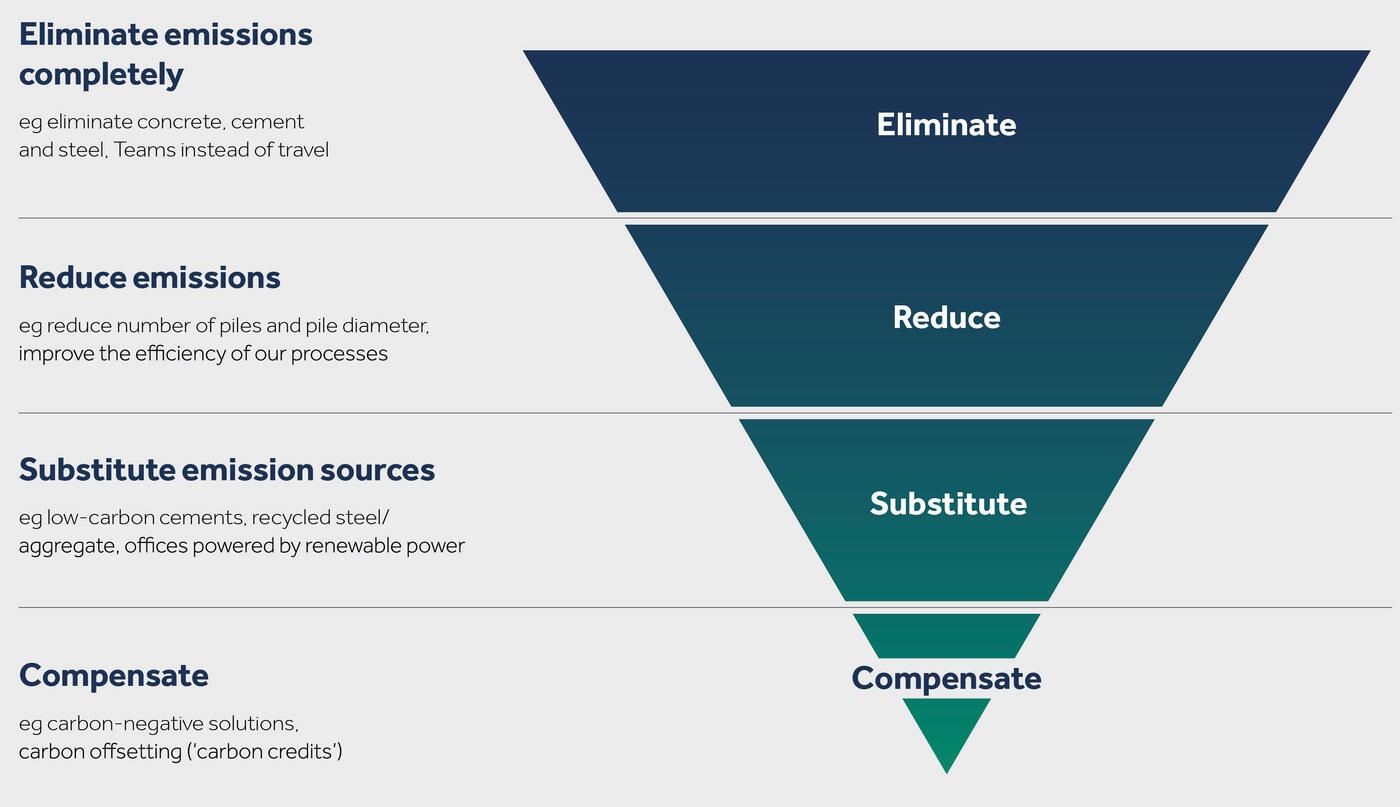
Case study
Keller’s first Global Sustainability Week
To coincide with United Nations Earth Day in April, Keller launched its inaugural Global Sustainability Week, promoting positive and practical ways to build a sustainable future.
Off the back of a successful Sustainability Week in North America in 2023, this year our divisional Team Planets – made up of volunteer sustainability champions from across the organisation – decided to go global, promoting Keller’s progress through a range of events and activities. These included webinars on topics such as sustainable solutions and mental health, as well as on-site ‘toolbox talks’ to encourage best practice.
For example, employees in EME and APAC got to hear from our charity partner UNICEF on their vital work, while North America held a fun sustainability-themed children’s art competition.
We also had fantastic participation from colleagues in our sustainability survey. For every entry, Keller committed to donate money to charity, eventually raising $15,000 for Bridges to Prosperity. This construction charity builds footbridges over otherwise impassable rivers to connect isolated communities to essential employment, education and healthcare services.
This week demonstrates that we’re putting sustainability at the heart of everything we do – making us a better company in the long run and ensuring we’re doing the right thing for the planet, our people and beyond.
Chief Sustainability Officer